Development of a mineral binder to substitute fossil-based adhesives in EWP
The project seeks to develop mineral-based binders with sufficient bonding performance to (partially) replace today’s resins and to create a more environmentally friendly, healthier, and more sustainable class of engineered wood products.
Factsheet
- Lead school School of Architecture, Wood and Civil Engineering
- Institute Institute for Building Materials and Biobased Products IBBM
- Research unit Materials and Life Cycle Assessment group FGWO
- Funding organisation Innosuisse
- Duration (planned) 01.01.2023 - 01.01.2026
- Project management Prof. Dr. Heiko Thömen
- Head of project Dr. Ali Shalbafan
- Project staff Christof Tschannen
- Partner Omya International AG
- Keywords EWP, Engineered wood products, mineral binder
Situation
Formaldehyde-based adhesives, as used in engineered wood products (EWP) today, are responsible for the majority of the EWP's CO2 emissions and are still considered problematic by many end users due to their formaldehyde emissions. Therefore, considerable work has been done in recent years on a new class of mineral binders. These binders have almost 80% reduced CO2 emissions compared to a urea-formaldehyde resin. Recent work at BFH has demonstrated that EWP with such binders can also be produced in a hot-pressing process and thus under short cycle times, and that the EWP produced have promising technical performance indicators.
Course of action
The aim of this project is to build on the existing knowledge and to develop a new mineral binder to produce EWP. Due to its better availability and the resulting avoidance of new global dependencies, especially on the magnesite-producing countries like China and Russia, this new binder is to be based on Omya International AG’s own raw material. The binder is to be heat-induced curing and initially designed for use in plywood production (global plywood production is about 129 million m3 per year). The panel product will have a binder content of less than 20% and will be designed as a direct substitute for conventionally produced plywood. The aim is to achieve mechanical properties comparable to those of conventional plywood for interior applications. The boards will also be tested for improved resistance to fire. The project is being handled by a strong consortium. As one of the world market leaders for industrial minerals, Omya International AG is strategically ideally positioned for the new development. And the Institute for Materials and Wood Technology IWH at BFH has extensive know-how in both mineral binders and wood-based panels technology.
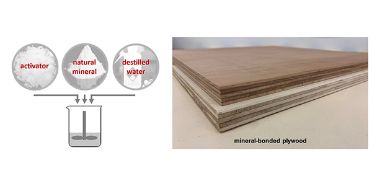